Are you tired of designing the technology of tomorrow, still building your electronic boards in a prehistoric way?
Posted on: Dec. 29, 2022, 11:18 p.m.
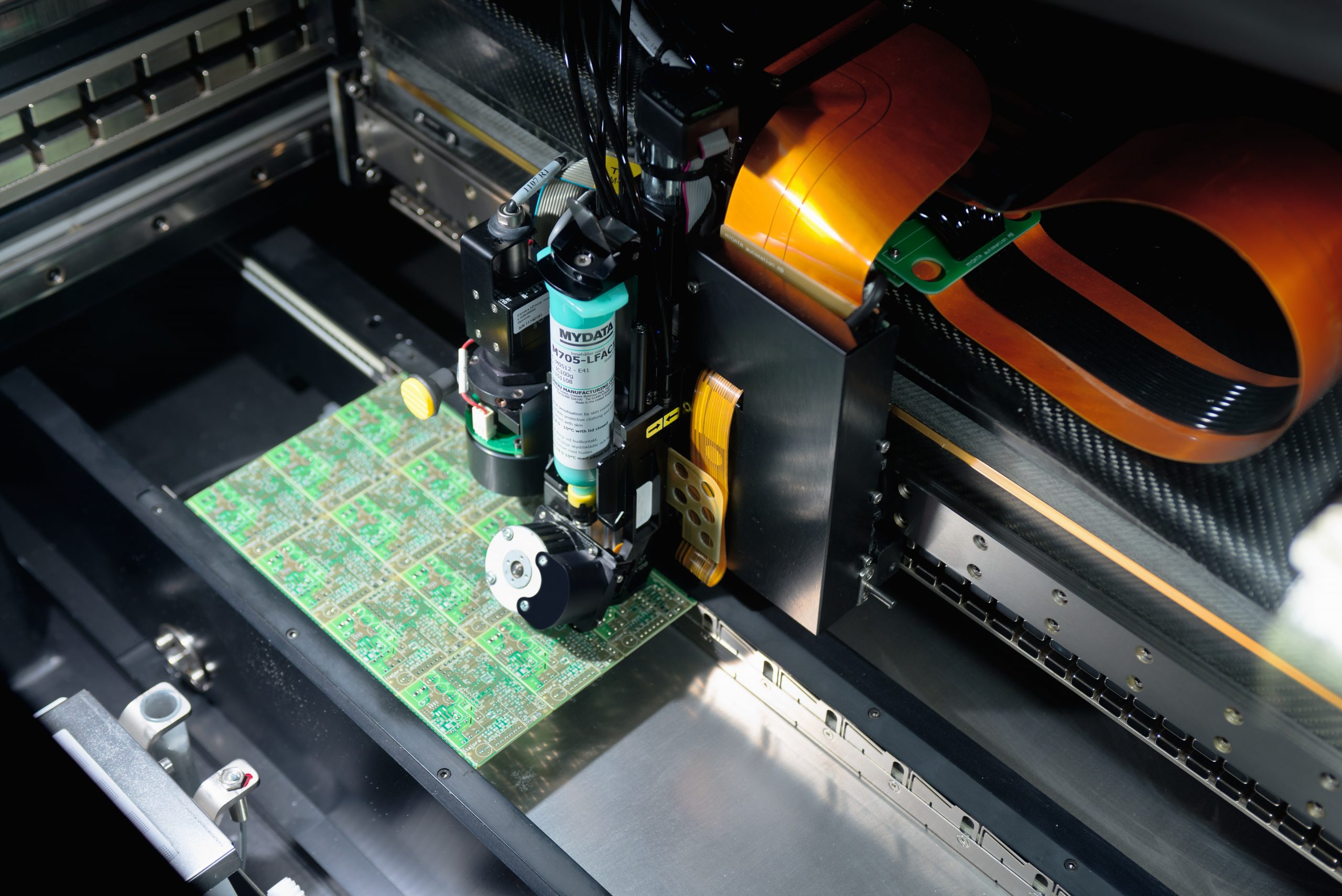
In this article you will find out how to get rid of the old system by reducing the production time of electronic boards by 68% and eliminating all inefficiencies.
The prototype you want to make will be ready in 1/3 of the time compared to how you are doing today.
Every time you have to send the electronic boards of the latest prototype that you have been working on for weeks into production, you are faced with a series of obstacles.
Aren't you tired of always dealing with incompetent suppliers who steal your precious time?
Obstacles that unfortunately until today you could not avoid since there was no alternative.
You'll soon understand what I'm talking about, because we had to face all these problems and, tired of the prehistoric method, we wanted to develop a system to speed up the production of electronic boards in small series.
Wouldn't it be great if there was a method to independently manage the production of your electronic board?
Immediately check the availability of the components, decide with a click to replace an unobtainable one, know exactly the production times and be amazed to discover that this new system costs less than the old one.
All this without having to write or call any supplier!
The system you use now is making you waste a lot of time
On the other side we had the same problem
You must know that we often worked with engineers from important multinationals who deal with managing the production of electronic boards and alongside whom we fought every day to be able to get those blessed boards built on time.
To get to the production of the electronic boards it was necessary to work for weeks and we always arrived at the last minute without knowing if the shot would hit or miss the target.
More or less the flow was this:
They required a quotation for an assembly, the availability of components in the warehouse and production availability based on the commitment of the assembly lines.
At this point in order to proceed we needed a little work on our part.
Two or three days of waiting . . .
When they received our answer, the dance of phone calls and email exchanges began towards the various Brokers for the missing components.
They then had to contact another supplier for the creation of the printed circuits and worry about being able to coordinate the deliveries of all the materials in order to take advantage of the production period that was reserved by us.
You may not be aware of it, but
Whoever assembles needs to define production slots for each customer because the preparation phases for production can take up to a couple of days.
Those who assemble electronic control units like us, especially for prototypes or small series, must necessarily plan the days in which the production lines will be dedicated to a certain product or a certain customer.
All this to say that if all the material does not arrive in time for the "work start" date, there is a risk of finding the lines busy and production can be postponed even by weeks.
In addition to the damage, there may be the added insult of having to pay a penalty for the machine downtime that has occurred.
Said this . . .
When we received the indications we proceeded to further checks; we checked if there had been any changes introduced and if all the components purchased were correct and compliant with the assembly.
More time wasted because . . .
Almost always further problems arose from the checks which triggered a new waltz of phone calls and e-mails.
Do you know a dog that bites its tail?
But that's not enough
Estimating the precise costs of an assembly was impossible for us and for our customers
If only we had a way to let our customers manage the production of electronic boards independently. . . with the possibility of verifying the availability of materials, production times and having certain costs right from the start
We have searched far and wide for a solution to rejuvenate this old way of building electronic boards but there is little we can do, when the solution does not exist we have to invent it and therefore we have invented it!
We thought of a solution that will allow you to save so much time that you can finally complete the Lego Death Star
This is how WEP was born, the first platform in Italy that allows you to easily and quickly manage the production of your electronic boards independently, without wasting time and without having to exchange 1000 emails with suppliers.
Are you curious, do you want to know more?
Find out how WEP works in the next article